Brass
Copper and zinc alloys can be individually adapted to different areas of application. By adding alloying elements Al, Mn, Si, Fe or Pb, the individual mechanical properties of the castings can be influenced.
The good foundry properties of the material in combination with our experience in the field of mold and core construction enable the production of thin-walled and complex castings.
The strengths of conventional steels, corrosion resistance, especially weathering, seawater resistance, high wear resistance and good machinability provide the designer with a cost-effective alternative for a wide range of possible applications.
CuZn38Al-C, CuZn37Al1-C, CuZn34Mn3Al2Fe1-C and CuZn16Si4-C have proved particularly useful as casting materials.
Copper and zinc alloys are not harmful to health, their surfaces have an antimicrobial effect.
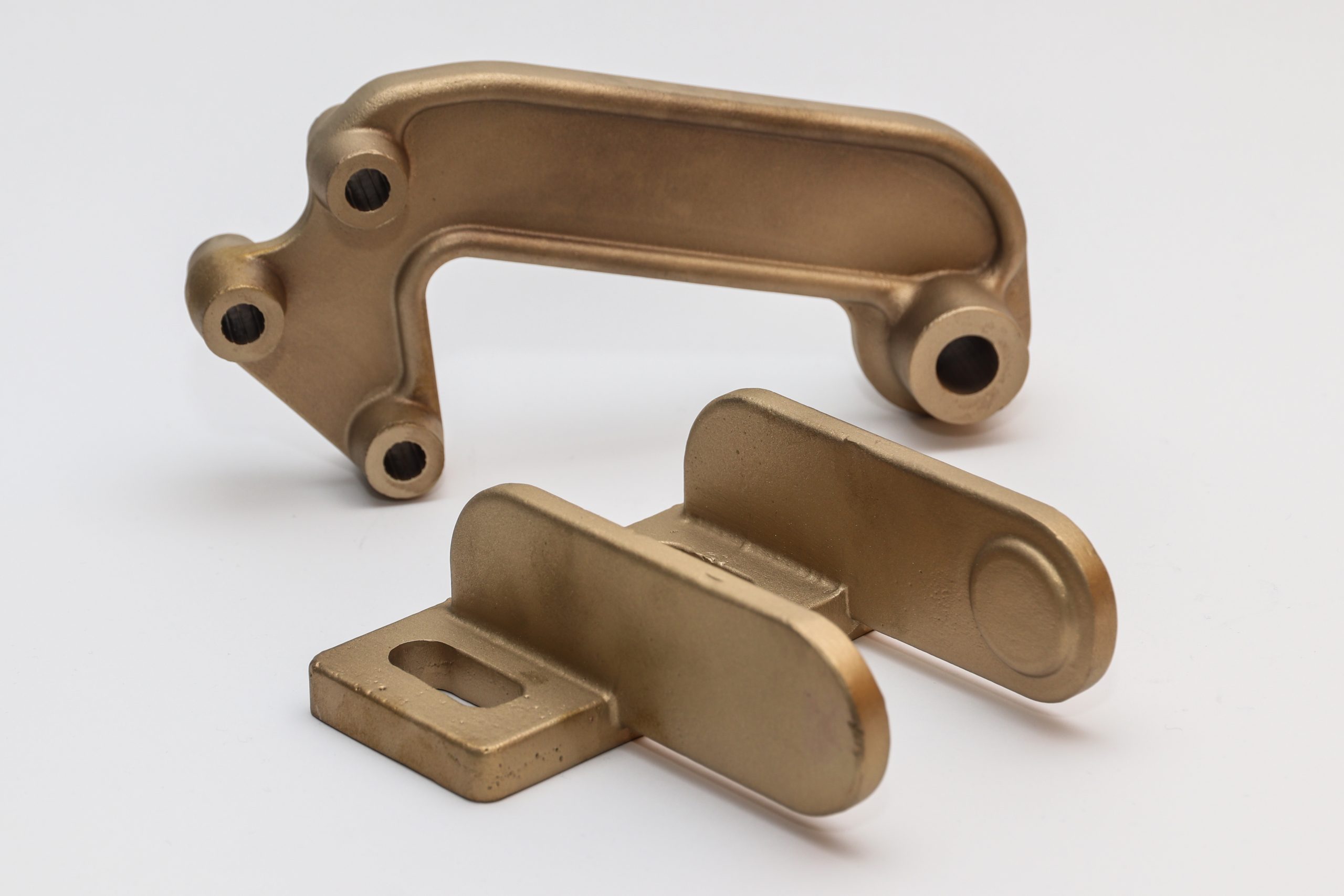
Technical use of brass:
• In the construction of machines and equipment, for example in transport technology, ventilation technology, in tool, energy and printing machines, in drive technology, robotics, automation …
• In the special construction of machines and equipment as a segment of bevel gears, gears and bevel gears.
• In the design of pumps such as suction pumps, pressure bodies, impellers, segment holders and housings and much more.
• In medical technology for milling arms, pipe bends or medical devices.
• We offer our customers individual copper and zinc alloys, which we develop especially according to requirements.
• By alloying various elements, it is possible to achieve the required mechanical properties for almost all possible applications.
• We will be happy to advise you on how to find the optimal material.
Aluminum bronzes
Copper and aluminum alloys are high-strength alloys. Therefore, they can be used as construction material in various fields. By adding Ni and Fe alloying elements, various properties of castings can be influenced, such as static and dynamic strength, resistance to cavitation erosion, or wear resistance.
The strength characteristics of alloys are affected not only by the composition of the alloy, but also by the casting process. When casting these materials into metal resp. copper molds, the strength characteristics of castings reach particularly high values. Copper and aluminum alloys have proven themselves in contact with a large number of media that are too aggressive for other copper materials.
The balanced Al-Ni ratio ensures a high level of corrosion resistance in environments such as:
• weakly acidic to weakly basic saline solutions (sulphite and bleaching solutions, potassium salt solutions)
• industrial wastewater
• Seawater and organic media (including acetic acid)
• Reduced and easily oxidizable mineral acids (diluted eg 10% hydrochloric acid, hydrofluoric acid 1% phosphoric acid and especially concentrated sulfuric acid)
• in an aggressive industrial environment near the sea or in an environment containing sulfur dioxide
CuAl10Ni3Fe2-C, CuAl10Fe5Ni5-C and CuAl11Fe6Ni6-C have proved particularly useful as casting materials.
Technical use of aluminum bronzes:
• In railway technology, for example in the construction of overhead lines such as spacers, buckles and suspension rope holders, as locking parts for doors and much more.
• In the design of suction pumps, pressure bodies, impellers, segment mounts and much more.
• In mechanical engineering for parts that must have high fatigue strength.
• In shipbuilding for seawater resistant applications where very high strength values are required.
We offer our customers individual copper and aluminum alloys, which we develop especially according to requirements.
By targeted variation of the alloying elements, the desired mechanical properties can be achieved for almost all possible applications.
We will be happy to advise you on finding the optimal material.
Copper-chromium alloy
Pure copper
The highest possible electrical and thermal conductivity can be achieved by casting in a metal mold using the appropriate quality of copper. The high conductivity values that can be achieved affect the degree of purity of the copper in combination with the manufacturing process. In pure copper castings, electric currents are then transmitted with low resistance.
The complex geometries of the castings are created by means of inserts and cores placed in the molds, which reduces the subsequent costs of machining. We will be happy to support you in the design of your product, which will be suitable for the casting process.
Copper-chromium alloy
The casting made of CuCr1-C is characterized by a combination of high strength and high conductivity for electricity and heat. Electrode holders and mechanically loaded contacts are often made of this material. In the case of alloy castings of this type, further processing such as mechanical polishing, galvanic plating is suitable.
Constructions made by cold copper casting can be found wherever electric currents flow.
As contact carriers, shorting rings, grounding contacts, contact fingers, high voltage switch parts,
Technical use of ECu copper:
• electrical engineering
• energy supply
• the design of the converter
• the construction of the transformer
• railway technology / overhead line construction
• for welding electrodes
• electronic mobility